Target of the Application
Open ABUTMENT in STL format and apply automatically toolpath.
We must consider 3 things:
“Abutment” ![]() | “Connectic” ![]() | “Hole” ![]() |
To produce abutment, we use always same tool for 100% of abutment. Turning Tool to do the OD: Insert holder is SVJBR – Insert is VBMT110302 – TOOL ID#2 Ball End Mill Tool D03 in Radial to do roughing at C0 and C180 – TOOL ID#5 Ball End Mill Tool D01.5 in radial to do rest machining and be sure that the finishing tool will not break – TOOL ID#3 Ball End Mill Tool D02 in axial to finish occlusion side (maximum depth is 5mm) – TOOL ID#6 Ball End Mill Tool D01.5 in Radial to Finish in 4Xs Abutment – TOOL ID#3 | To produce Connectic Back Turning Tool – TOOL ID#3 Flat End mill D04 to do the hexagon – TOOL ID#4 Parting Tool – TOOL ID#1 | To produce Hole: Spotting Drill D4 - TOOL ID#7 Drilling tool (this tool is shape tool) 2 different diameters. This tool can be change according to each implant provider and size – TOOL ID#8 / – TOOL ID#9 / – TOOL ID#10 |
NB:
G code for Holes and Connectic is not manage by the CAM.
Holes and Connectic are managed by sub program.
ToolPath for Holes and Connectic are always the same according to each provider
Inisde the NC file we have “new REFERENCE POINT” here the variable used is #100
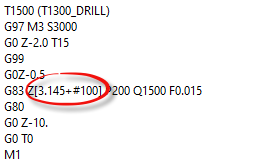
Current machine in production:
Star – SB-20R TypeG
Star - SR 20 JII Type B
Pending machine
Citizen L20
Chiron FZ08MT